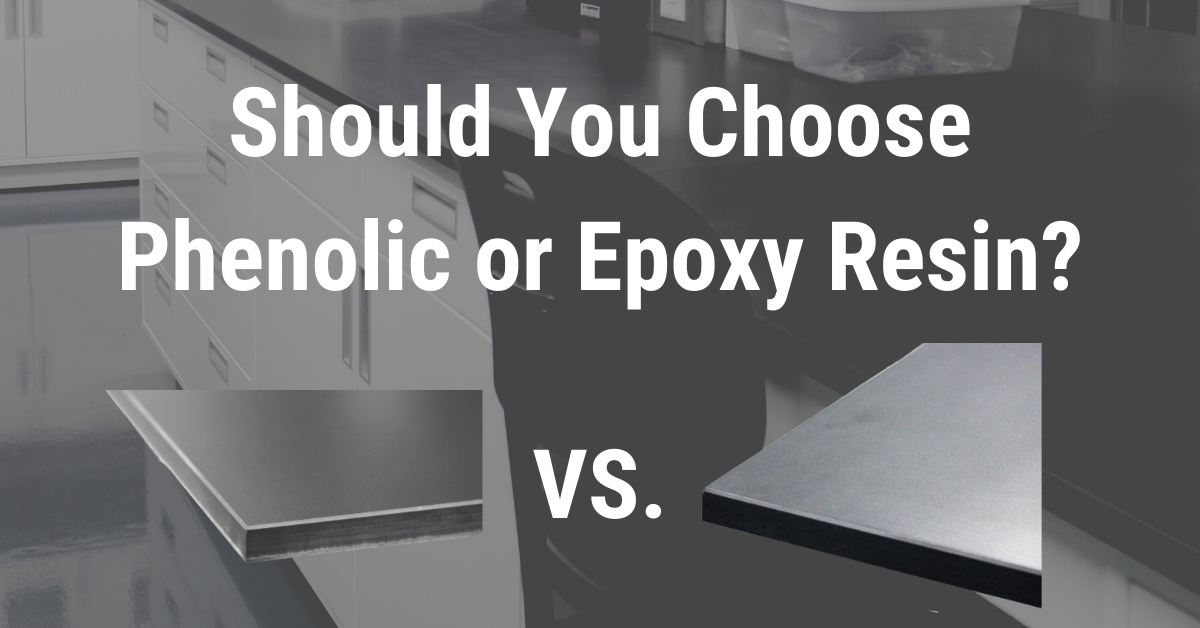
Should You Choose Phenolic or Epoxy Resin?
Phenolic Resin vs. Epoxy Resin Test Results
List of Chemicals Tested on Both Phenolic and Epoxy:
After 24-hours exposure, areas are washed with water, then a detergent solution and finally with isopropyl alcohol. Materials are then rinsed with distilled water and dried with a cloth.
- Amyl Acetate
- Ethyl Acetate
- Acetic Acid, 98%
- Acetone
- Acid Dichromate, 5%
- Butyl Alcohol
- Ethyl Alcohol
- Methyl Alcohol
- Ammonium Hydroxide, 28%
- Benzene
- Carbon Tetrachloride
- Chloroform
- Chromic Acid, 60%
- Cresol
- Dichloracetic Acid
- Dimethylformamide
- Dioxane
- Ethyl Ether
- Formaldehyde, 37%
- Formic Acid, 90%
- Furfural
- Gasoline
- Hydrofluoric Acid, 37%
- Hydrofluoric Acid, 48%
- Hydrogen Peroxide, 28%
- Tincture of Iodine
- Methyl Ethyl Ketone
- Methylene Chloride
- Monochlorobenzene
- Naphthalene
- Nitric Acid, 20%
- Nitric Acid, 30%
- Nitric Acid, 70%
- Phenol, 90%
- Phosphoric Acid, 85%
- Silver Nitrate, Saturated
- Sodium Hydroxide, 10%
- Sodium Hydroxide, 20%
- Sodium Hydroxide, 40%
- Sodium Hydroxide, Flake
- Sodium Sulfide, Saturated
- Sulfuric Acid, 33%
- Sulfuric Acid, 77%
- Sulfuric Acid, 96%
- Sulfuric Acid 77%, and Nitric Acid 70%, equal parts
- Toluene
- Trichloroethylene
- Xylene
- Zink Chloride, Saturated
Scoring Criteria
0 = No effect, 1 = Excellent, 2 = Good, 3 = Fair
Test Results – Phenolic Resin
Phenolic resin scored 0 (No effect) for the follow chemicals:
- Amyl Acetate
- Ethyl Acetate
- Acetic Acid, 98%
- Acetone
- Butyl Alcohol
- Ethyl Alcohol
- Methyl Alcohol
- Benzene
- Carbon Tetrachloride
- Chloroform
- Dimethylformamide
- Dioxane
- Ethyl Ether
- Formaldehyde, 37%
- Furfural
- Gasoline
- Hydrofluoric Acid, 37%
- Hydrogen Peroxide, 28%
- Methylene Chloride
- Naphthalene
- Nitric Acid, 20%
- Nitric Acid, 30%
- Nitric Acid, 70%
- Phosphoric Acid, 85%
- Silver Nitrate, Saturated
- Sodium Hydroxide, 10%
- Sodium Hydroxide, 20%
- Sodium Hydroxide, 40%
- Sodium Hydroxide, Flake
- Sodium Sulfide, Saturated
- Sulfuric Acid, 33%
- Sulfuric Acid, 77%
- Sulfuric Acid, 96%
- Sulfuric Acid 77%, and Nitric Acid 70%, equal parts
- Toluene
- Trichloroethylene
- Xylene
- Zink Chloride, Saturated
Phenolic resin scored 1 (Excellent) on:
- Acid Dichromate, 5%
- Ammonium Hydroxide, 28%
- Chromic Acid, 60%
- Cresol
- Dichloracetic Acid
- Formic Acid, 90%
- Hydrofluoric Acid, 48%
- Tincture of Iodine
- Methyl Ethyl Ketone
- Monochlorobenzene
- Phenol, 90%
Phenolic resin did not score 2 (Good) or 3 (Fair) on any test. This indicates that phenolic is very chemical resistant to nearly all commonly found reagents.
Test Results – Epoxy Resin
Epoxy resin scored 0 (No effect) on:
- Amyl Acetate
- Ethyl Acetate
- Acetic Acid, 98%
- Acid Dichromate, 5%
- Butyl Alcohol
- Ethyl Alcohol
- Methyl Alcohol
- Ammonium Hydroxide, 28%
- Benzene
- Carbon Tetrachloride
- Chloroform
- Cresol
- Dichloracetic Acid
- Dimethylformamide
- Dioxane
- Ethyl Ether
- Formaldehyde, 37%
- Formic Acid, 90%
- Furfural
- Gasoline
- Hydrogen Peroxide, 28%
- Methyl Ethyl Ketone
- Monochlorobenzene
- Naphthalene
- Nitric Acid, 20%
- Nitric Acid, 30%
- Nitric Acid, 70%
- Phenol, 90%
- Silver Nitrate, Saturated
- Sodium Hydroxide, 10%
- Sodium Hydroxide, 20%
- Sodium Hydroxide, 40%
- Sodium Hydroxide, Flake
- Sodium Sulfide, Saturated
- Toluene
- Trichloroethylene
- Xylene
- Zink Chloride, Saturated
Epoxy resin scored a 1 (Excellent) on:
- Acetone
- Tincture of Iodine
- Methylene Chloride
- Phosphoric Acid, 85%
- Sulfuric Acid, 33%
- Sulfuric Acid, 77%
- Sulfuric Acid 77%, and Nitric Acid 70%, equal parts
Epoxy resin scored a 2 (Good) on:
- Chromic Acid, 60%
And a 3 (Fair) on:
- Hydrofluoric Acid, 37%
- Hydrofluoric Acid, 48%
- Sulfuric Acid, 96%
Phenolic Resin Physical Property Testing
* Appearance Rating 5 = No Change
Test-ID – Test Description – Phenolic Resin Results
EN 438-2:10 – Resistance to Surface Wear – >=150 Revolutions (lnital Point)
EN 438-2:21 – Resistance to Impact – 0.4 Indention Diameter (mm); No Cracks or Scoring
EN 438-2:25 – Resistance to Scratch – 5 Rating (Based on Load)
EN 438-2:16 – Resistance to Dry Heat (320″F) – 5 Appearance*
EN 12721 – Resistance to Wet Heat (212’F) – 5 Appearance*
EN 438-2:12 – Resistance to Immersion in Boiling Water – 5 Appearance*; 0.4 Mass Increase %; 1.9 Thickness Increase %
EN 438-2:17 – Dimensional Stability in Elevated Temperature – 0.05 Longitudinal (Parallel)%; 0.05 Transversal (Perpendicular) %
EN 438-2:26 – Resistance to Staining (Appearance Rating) – 5 Acetone; 5NaOH; 5 Hydrogen Peroxide (H202 3%)
ASTM G53/ EN 4382:27 – Resistance to Color Change – 5 Appearance* (Grey Wool Scale)
EN 438-2:24 – Resistance to Crazing – 5 Appearance*
ASTM 638-08/EN ISO 178 – Modulus of Elasticity – >=1.85e6 psi
ASTM 790-08/EN ISO 178 – Flexural Strength – >=2.87e4 psi
ASTM 638-08/EN ISO 527-2 – Tensile Strength – >=2.71e4 psi
ASTM 792-08/EN ISO 1183 – Density – >=86.15 lbs/ft^3
Should You Choose Epoxy or Phenolic?
In summary – phenolic performers better on average at standing up to common laboratory chemicals. It shows no weaknesses at all. Epoxy resin on the other hand has a few vulnerabilities.
The 2 and 3 rated chemicals for epoxy resin – Chromic acid (60%), hydrofluoric acid (37%, 48%), and sulfuric acid (96%), should be handled with extreme care in labs using epoxy resin countertops. If you are using those frequently, we highly recommend considering phenolic resin as the material for your work surfaces and potentially even your casework and storage.
Epoxy resin held up stronger compared to phenolic with tested with acid dichromate (5%), Ammonium hydroxide (28%), cresol, dichloracetic acid, formic acid (90%), methyl ethyl keytone, monochlorobenzene, and pheonl (90%), but only slightly.
That being said both are an excellent choice for work surfaces on lab casework and tables. We recommend phenolic resin in all cases as it is more cost-effective, easier to obtain, allows for shorter lead times, and is in fact stronger against most chemicals. We may all look back in a decade or two and epoxy resin, despite being only slightly less effective, will be entirely replaced by phenolic.